Single-stage blowers and compressors
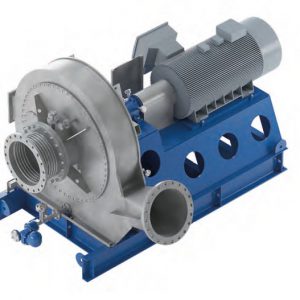
F1 Series
Single-stage blowers and compressors
Our F1 Series covers the largest range of radial blowers and compressors within the FIMA product series. As the best-selling series, it offers a wide range of products for diverse industries and application areas.
VARECO
(Vapor recovery compressor)
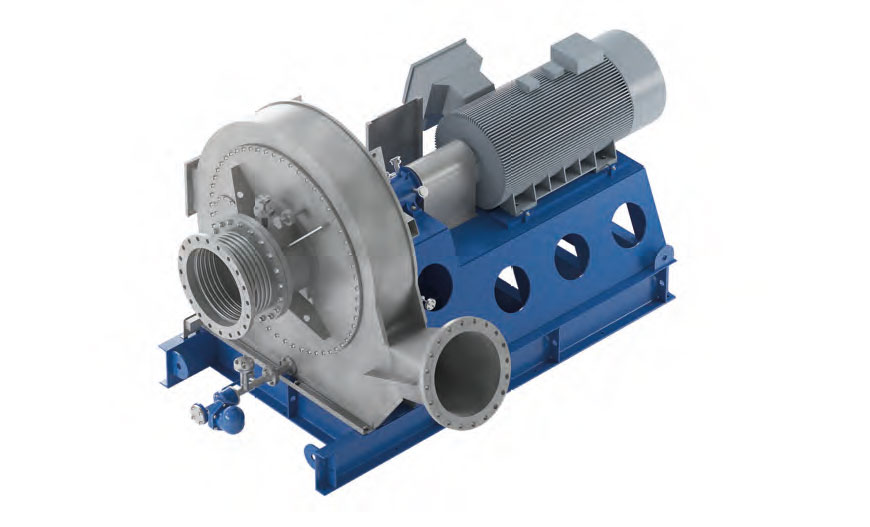
During the closed process of liquid evaporation, the vapor is fed through our VARECO, where its temperature and energy level are increased, and then fed back to the process. Thus, its valuable energy is not lost. The self-contained process allows volatile liquids to be evaporated while valuable products are retained.
Our VARECO is used in the chemi-cal industry in recovery processes for alcohols such as isopropanol and methanol. One example of its application is in the production of biofuels.
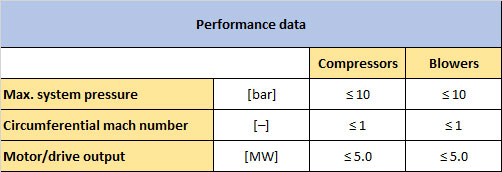
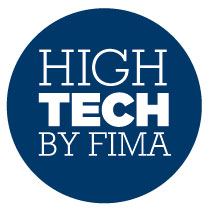
SULCO
(Sulfur compressors)
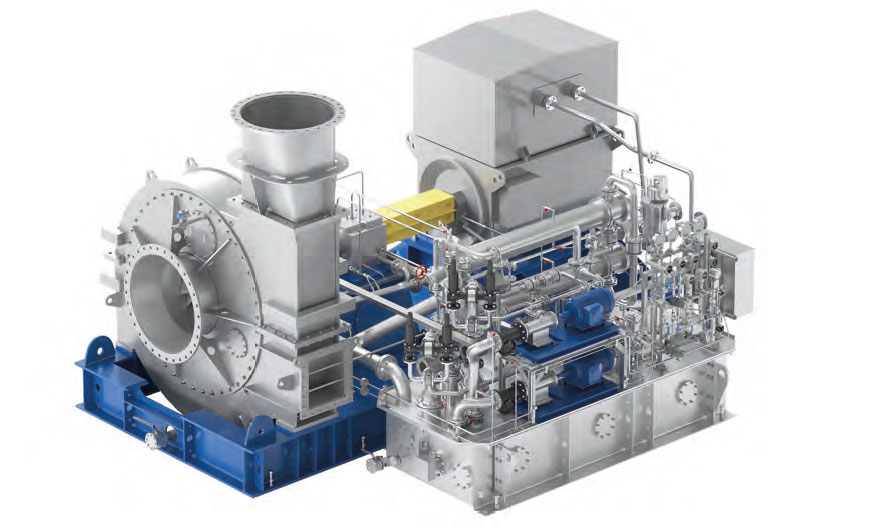
Our SULCO fans are used in sulfuric acid plants, sulfur combustion, acid regeneration, metallurgical processes, and numerous other applications in the sulfur industry.
In the production of sulfuric acid (H2SO4), the machines and the entire process system are exposed to highly aggressive acidic substances. We especially take this into account in designing our state-of-the-art machines. Our main gas blowers and combustion air fans guarantee maxi-mum safety, availability, reliability, and stability.
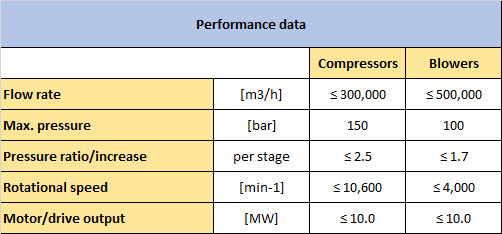
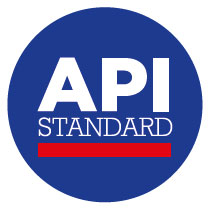
Polyethylene (PE)
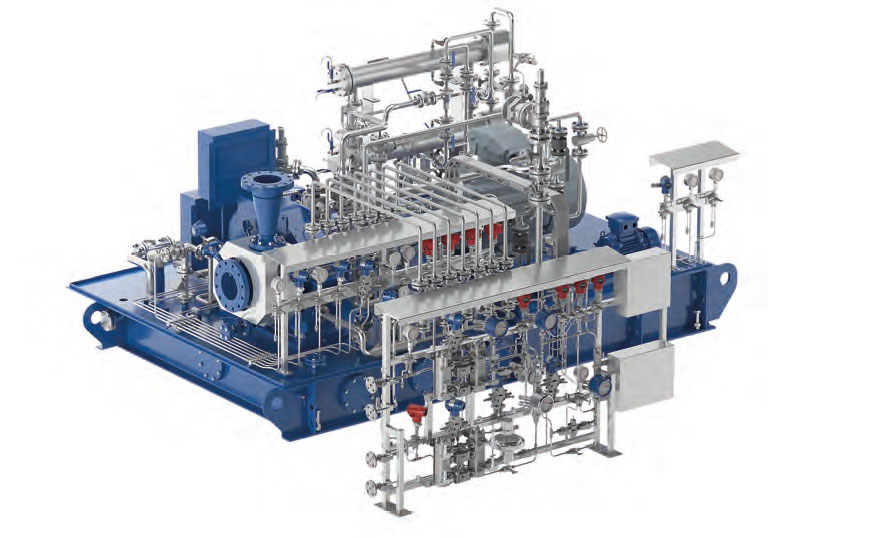
The plastic polyethylene (PE) is an extremely versatile product of the chemical industry. PE is used to make films of all kinds, beverage packaging, canisters, and even pipe jackets. The partially crystalline, nonpolar thermoplastic is divided up into different main types based on density. Through the selection of the polymerization conditions, the molecular weight, molecular weight distribution, kinetic chain length, and degree of polymerization are affected.
Our F1 Series single-stage compressors are used in applications such as the licensed “Innovene G” process from Ineos for the production of linear low-density polyethylene (LLDPE). FIMA supplies the ejector boosters and the ethylene compressors for this process.
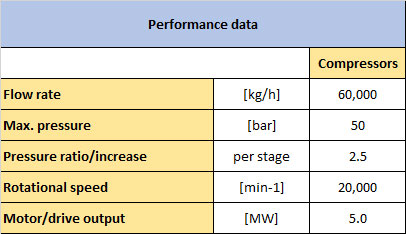
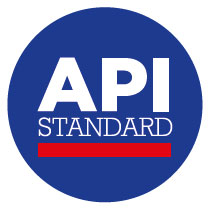
Polypropylene (PP)
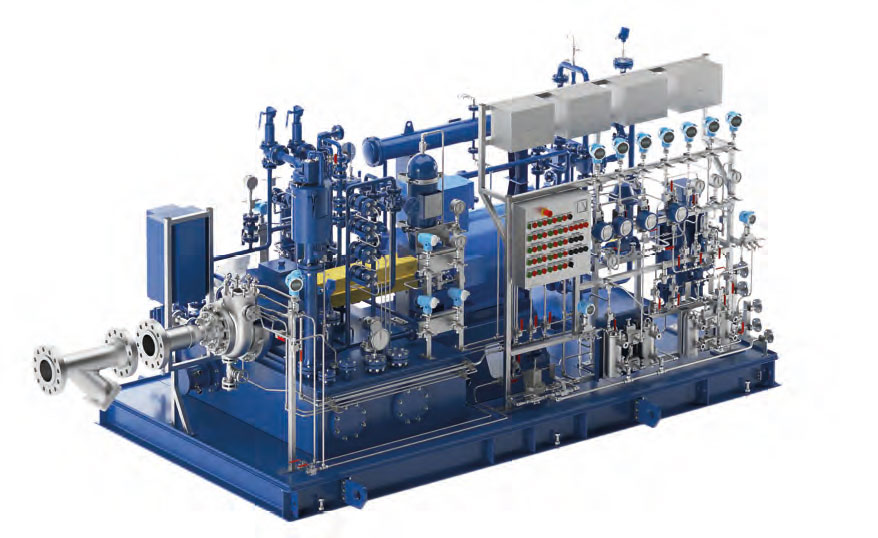
Compared with PE plastic, polypropylene (PP) is harder, is stronger, and can withstand higher thermal loads. Thanks to its special properties, PP has an extraordinarily wide range of applications. It is used in everything from vehicle interiors to food and cosmetics packaging, to pressure and drainage pipes.
The licensed Novolen process from Lummus Novolen Technology for producing PP is just one example of the use of recycle gas compressors from FIMA. In general, these compressors return the unconverted propylene gas to the reactor. Smaller single-stage compressors are often used for homomer plants. So-called cascade compressors are also used in PP production. They are installed in the multistage variant (see FIMA F3 Series).
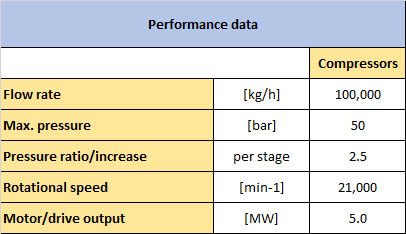
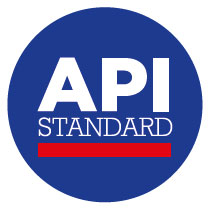
CCR UOP
(Continuous catalytic reforming)
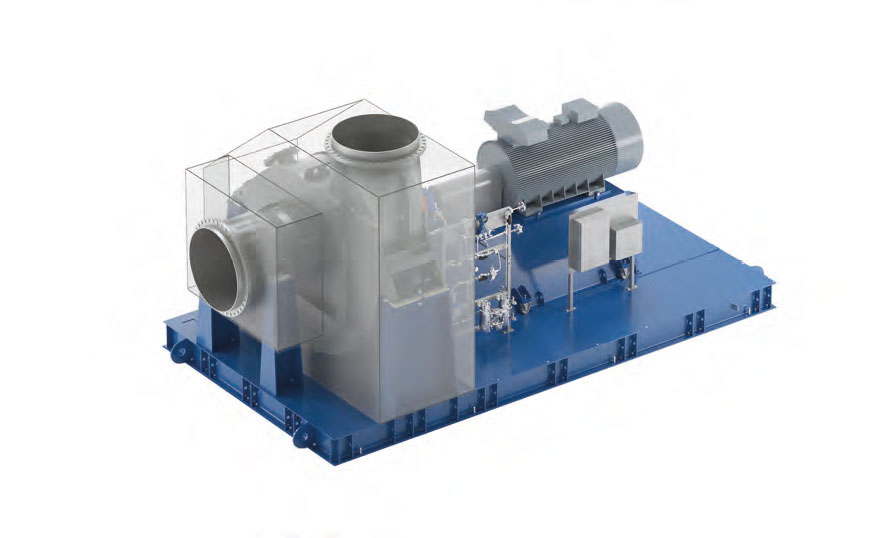
Catalytic reforming is a refining process in which aromatic compounds and branched alkanes are produced. The aim is to increase the octane number and produce higher-grade compounds. The reformate, or main liquid product, consists primarily of benzene, toluene, xylenes, aromatics, and alkane compounds.
In the licensed UOP system, the four reactors are stacked. The catalyst flows from the top of the first reactor to the bottom of the fourth reactor due to gravity alone.
FIMA supplies fans for the CCR PlatformingTM process and the CCR OleflexTM process. Hot-gas, or regenerative, blowers operated at a process temperature of approximately 600 °C are mainly used here. Apart from the main blower, fines removal blowers and cooler blowers are integrated and are available from FIMA for all UOP unit sizes.
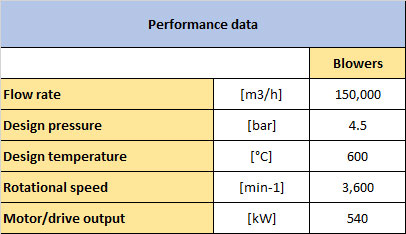
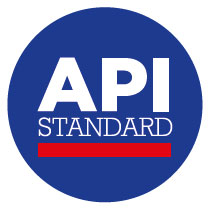
CCR Axens
(Continuous catalytic reforming)
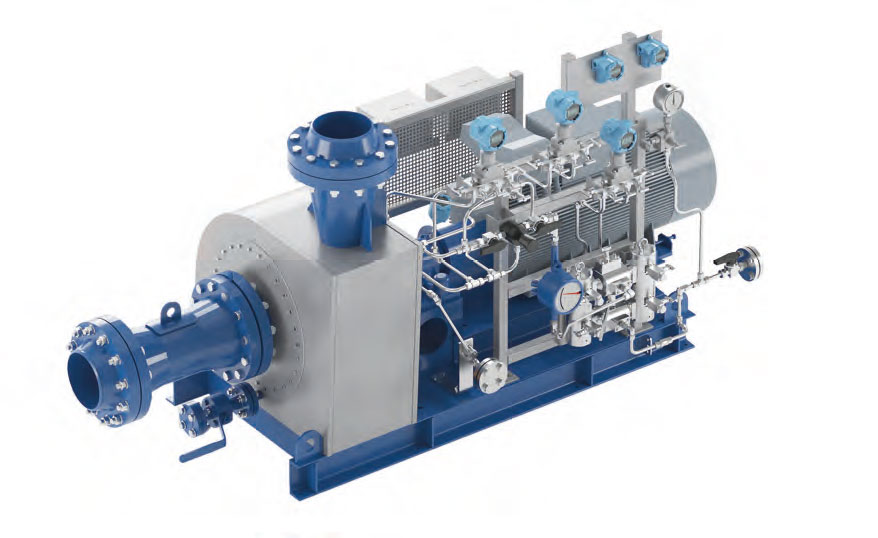
With the licensed CCR process from Axens, too, the goal is to increase the octane number and at the same time generate higher-quality aromatics and alkane compounds.
Axens uses a horizontal reactor setup similar to that used in the semi-regenerative process. The catalyst is transported by a lift system from the bottom of one reactor to the top of the next reactor. The cleaning and regeneration of the catalyst plays an important role in the process.
FIMA recirculation blowers are used to maintain and accelerate the regeneration process in the reactor.
In addition, FIMA elutriation blowers are used in a secondary process for removal of oxidation residues and dust from the regenerated catalyst.
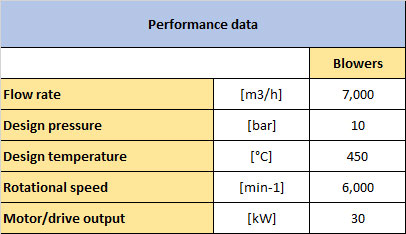
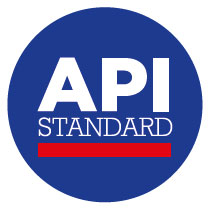
Methylene diphenyl diisocyanate (MDI)
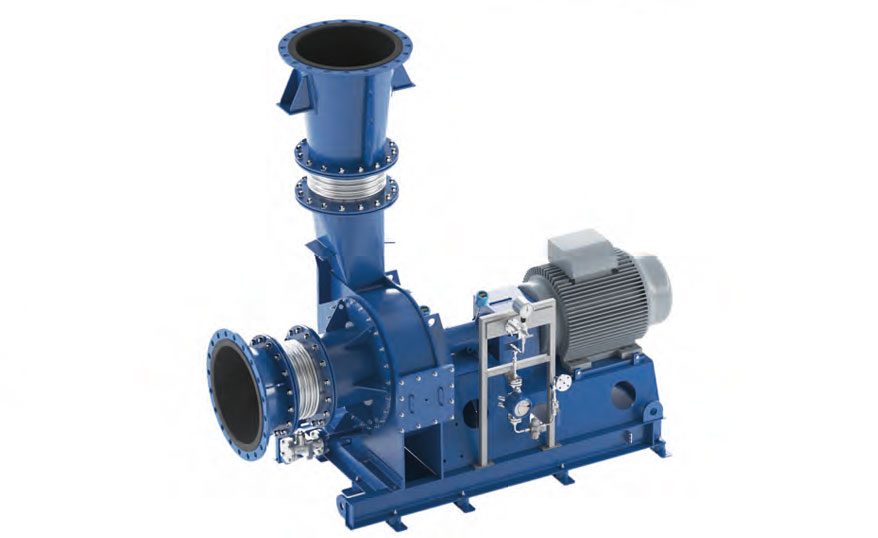
As chemical compounds from the group of aromatic isocyanates, methylene diphenyl diisocyanates are normally mixtures of several constitutional isomers. They differ in terms of the positions of the isocyanate groups. MDI is one of the most commonly produced isocyanates worldwide and is a key raw material for the production of polyurethane, polyamide and flexible foam, insulating foam, and adhesives.
FIMA supplies single-stage radial blowers for the production of MDI. Products include containment, air extraction, and exhaust gas fans. The machines are manufactured from high-grade materials and realized in sophisticated designs.
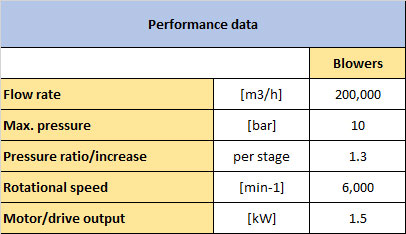
Toluene-2,4-diisocyanate (TDI)
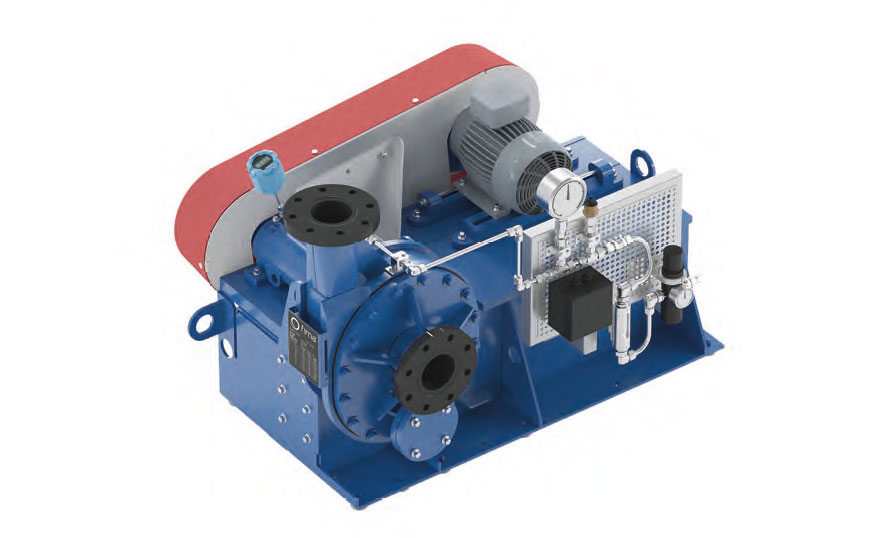
TDI is another important isocyanate besides MDI and a key intermediate in the plastics industry. It is produced either by nitration and subsequent hydrogenation or by oxidative dehydrogenation of formamides. TDI is needed in the chemical industry for the production of adhesives, foam materials for mattresses and upholstery, polyurethanes, elastomers, coatings, and high-grade paints as well as for the production of lubricants.
Due to the phosgene in the gas mixture, the fans must meet extremely high tightness and material requirements, which our machines can easily do. As exhaust gas, air extraction, or containment fans in the TDI production process, our machines provide the optimal solutions for the chemical process industry.
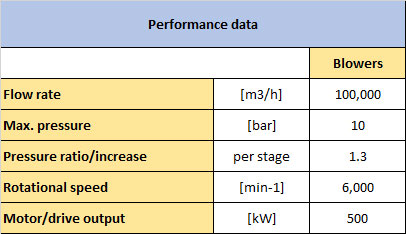
Nitrogen (N2)
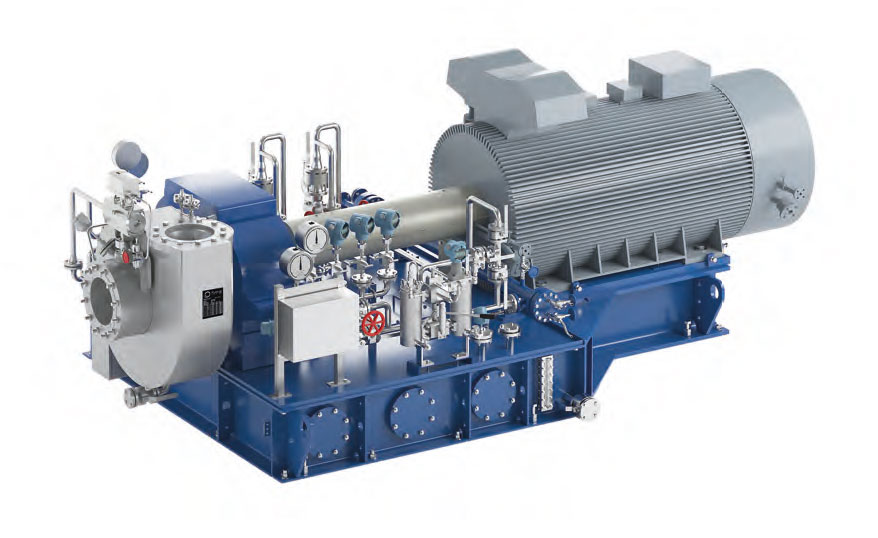
Nitrogen is an odorless and colorless gas used in a multitude of applications. For example, it is a main component in fertilizers and refrigerants and is used in its purest form for inerting.
FIMA fans and compressors are also used in combination with nitrogen in a multitude of processes: as regenerative gas blowers in polymerization processes for regenerating nitrogen, as nitrogen booster compressors in steel production, and as startup blowers for inerting, e.g., of methanol and hydrogen plants.
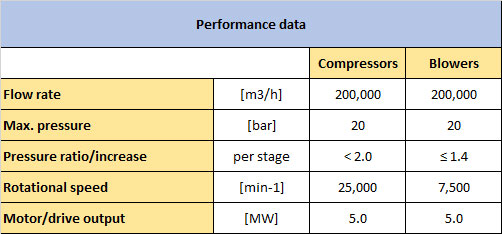
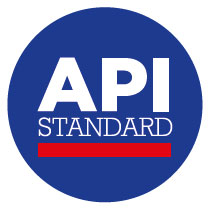
Hydrogen (H2)
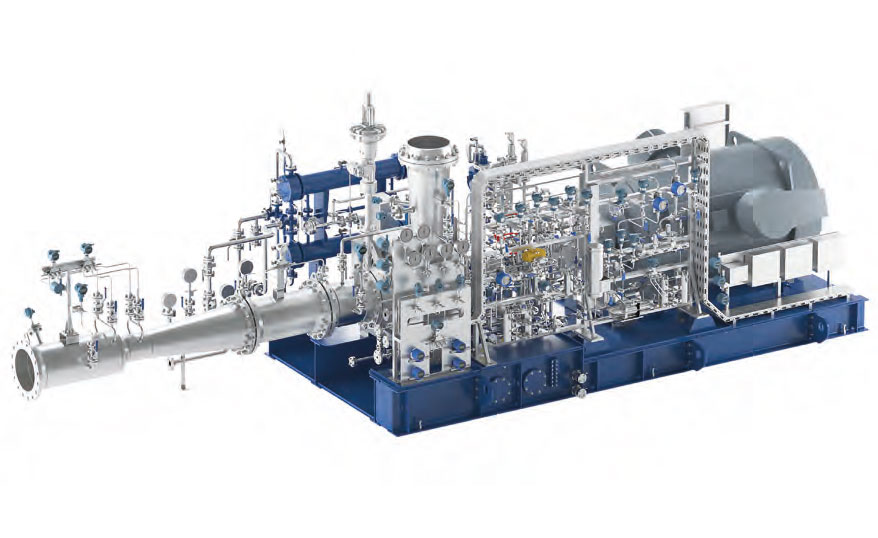
Hydrogen is one of the most important chemical elements and is a component of nearly all organic compounds. In response to the challenges of the energy transition, numerous new hydrogen-based processes are emerging, thereby building on the already significant role of hydrogen in numerous chemical processes.
One example is oxo synthesis, also known as hydroformylation. The large-scale process is used to produce aldehydes. Hydrogen serves as one of the starting products of the process. The resulting aldehydes are usually hydrogenated to form alcohols and are ultimately used as plasticizers, raw materials for laundry detergents and cleaning agents, or solvents. Because the process gas has a high hydrogen content, the material’s resistance to hydrogen embrittlement by the medium poses a special challenge.
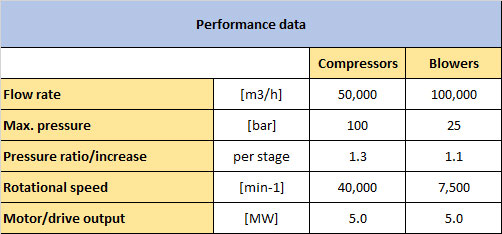
*Data based on gas mixture with molar mass of 10 g/mol
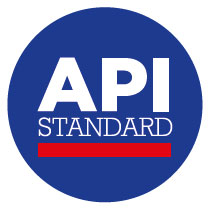
Chlorine gas (Cl2)
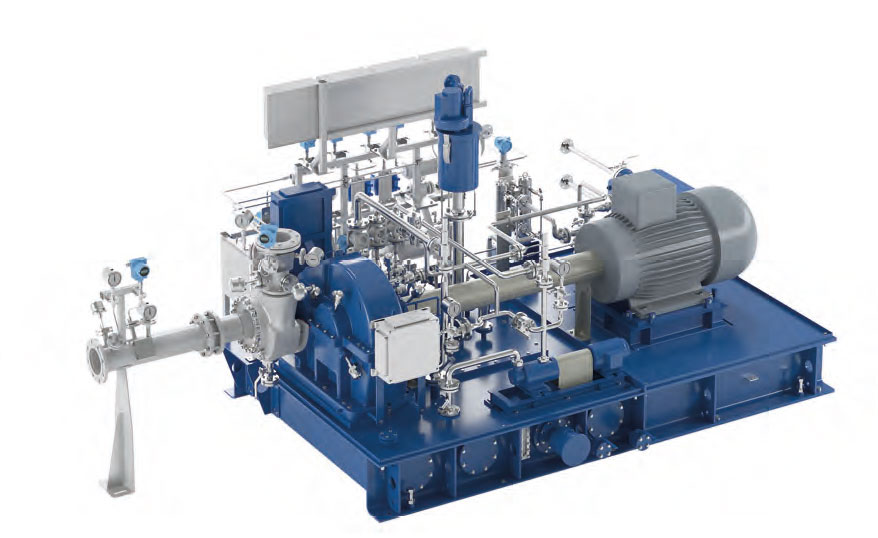
Due to its high reactivity, chlorine (Cl2) is an important basic chemical in the chemical industry. The aggressive green-yellow gas with a pungent odor is used for the production of organic and inorganic compounds such as hydrochloric acid or chlorides. It is also used as an oxidizing agent, a bleaching agent, and a disinfectant. Chlorine gas reacts with minute amounts of water (e.g., humidity) to form hydrochloric acid and is therefore highly corrosive to most metals when wet.
FIMA chlorine gas compressors are used, for example, in rubber production plants. The machines compress the chlorine gas needed by the process for the reactor. They are generally suitable for all chemical processes in which chlorine gas is transported.
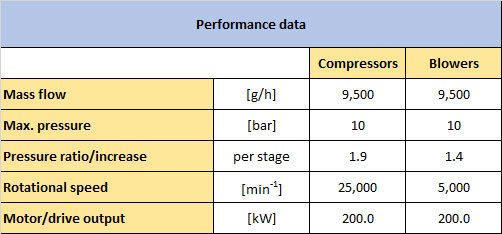
Nitric acid (HNO3)
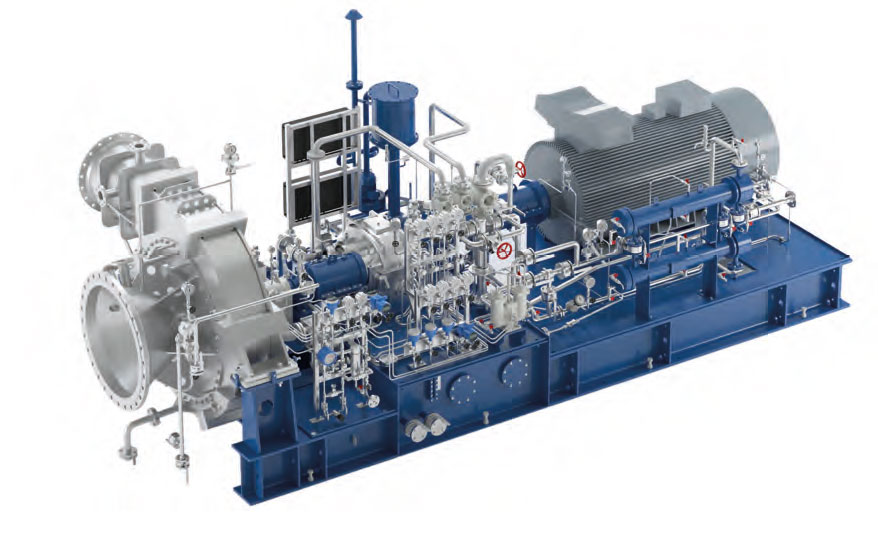
Nitric acid is one of the three most important basic chemicals in the chemi-cal industry. It is produced by catalytic oxidation of ammonia in the Oswald process. Nitric oxide is produced as an intermediate product, which reacts with oxygen to form nitrogen dioxide, which then reacts with water to form nitric acid. As a starting product for the Oswald process, ammonia is produced from natural gas and air in the Haber–Bosch process. FIMA also supplies blowers and compressors for this process.
Our machines are also used as NOx blowers in nitrite plants, where they transport the gaseous oxides of nitrogen (NOx). In this waste-free process, NOx is removed from the exhaust air and recovered. For this process, FIMA supplies exhaust gas and neutralization blowers.
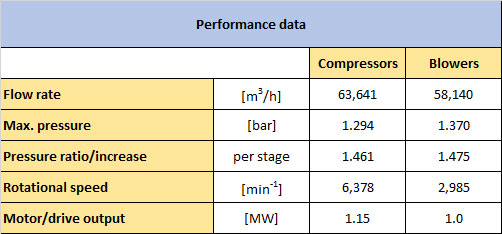
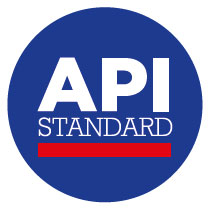
Acid recovery plant (ARP)
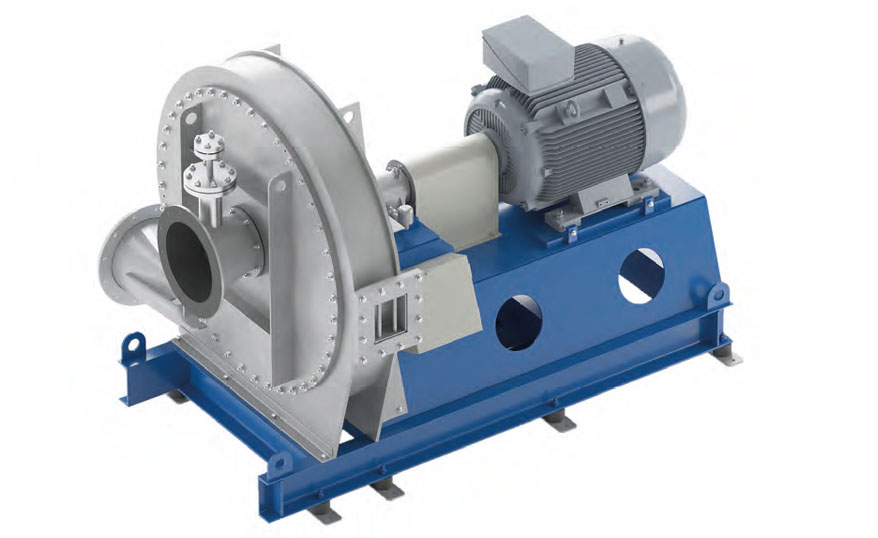
When steel is heated or rolled, an adherent blue-green layer composed of different iron oxides forms on the surface of the metal. This so-called mill scale can cause corrosion in downstream processing steps and therefore has to be removed. Pickling is used to free the metal from the layer of scale (bright pickling).
The contaminated iron-rich acid is converted in a reactor (spray roasting or fluidized bed process) and separated from the iron content in an acid regeneration plant. The regenerated acid is then returned to the pickling process. In the acid regeneration process, FIMA industrial fans are used as exhaust gas and flue gas blowers. Through the recycling of the hydrochloric acid, FIMA contri-
butes to a closed process cycle.
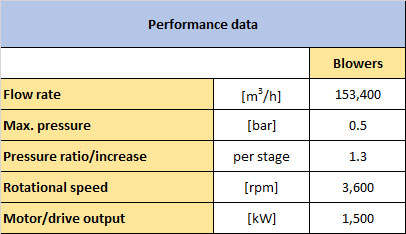
Highly dispersed pyrogenic silica
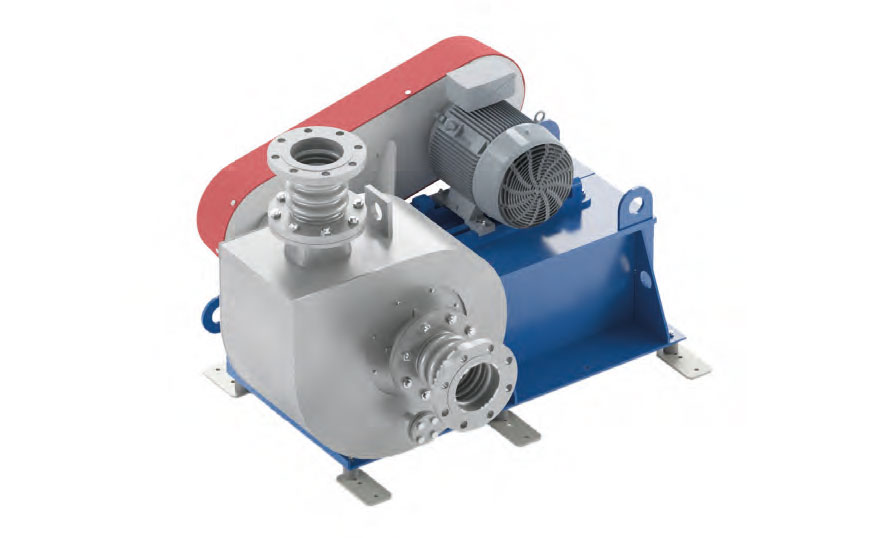
In chemical terms, pyrogenic, or fumed silica is an extremely pure amorphous silicon dioxide (SiO2). It exists as a loose, voluminous white powder. It can be found, for example, in dyes, toners, food, and pharmaceutics and is used in many everyday products. It is also used as a corrosion inhibitor in paints and is frequently used to modify rheological properties.
A variety of FIMA blowers are used in the silica production process. Because hydrochloric acid is a byproduct of production, some of the blowers are exposed to extremely harsh process conditions. Examples are the process gas blowers 1 & 2 and the exhaust blowers 1 & 2. In both cases, the two fans are connected in series. In this application, the conveyed gas has a very high hydrochloric acid (HCl) content.
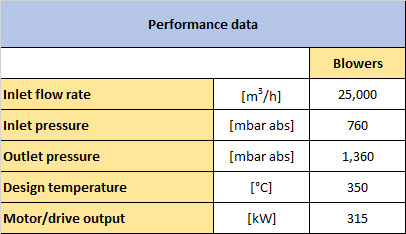
Fluidized bed drying
(Pharmaceutical blowers)
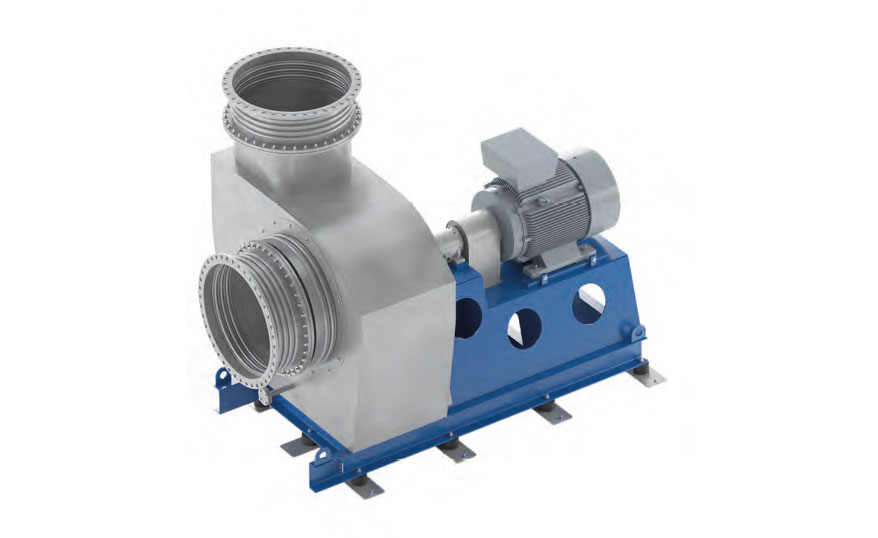
A widespread and commonly used drying method in the pharmaceutical industry is fluidized bed drying. This technical process is used to dry solids. A bed of solid particles such as powders, granules, or even pellets, tablets, or capsules is kept in motion by an upward flow of air. This airflow can be heated and thus transport away moisture in or on the particles and dry the product.
The centrifugal blowers are used for drying solids in the pharmaceutical industry. They can also be made of austenitic stainless steel (1.4404) or other materials.
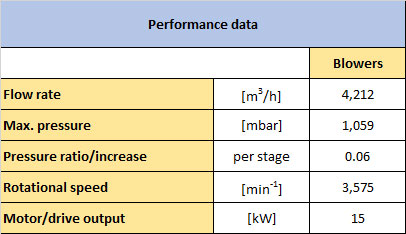
Liquefied natural gas
(LNG)
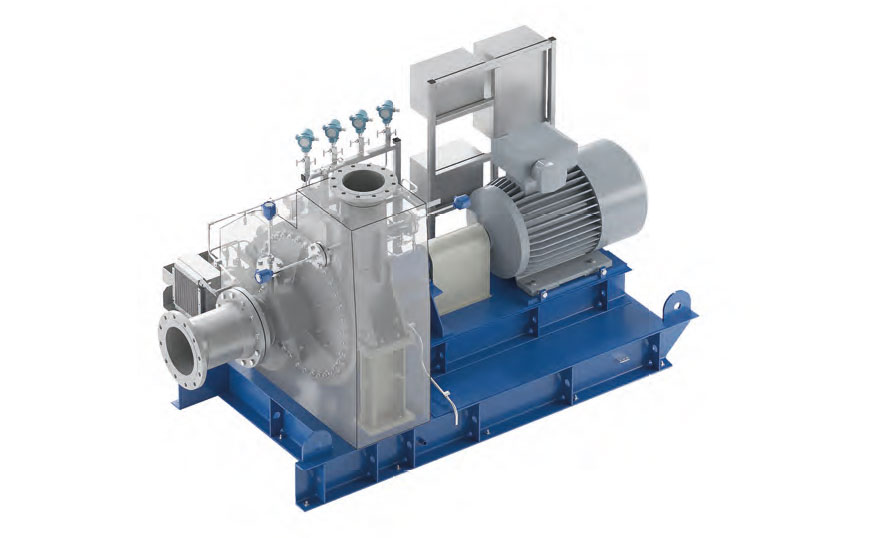
Liquefied natural gas (LNG) is natural gas that has been liquefied by being cooled down to −161 to −164 °C
(112 to 109 K). LNG has about one six hundredth of the volume of gaseous natural gas and therefore offers great advantages, especially for transport and storage. In a gas liquefaction plant or LNG terminal, the natural gas is stored, processed, and finally liquefied. The LNG is then pumped onto special ships, which move it to another LNG terminal.
FIMA boil-off gas (BOG) compressors and blowers are used to ensure that there is no negative pressure or vacuum in the tanks of the transport ship during unloading. They transport boil-off gases (BOG) from the LNG storage tanks back to the transport ship.
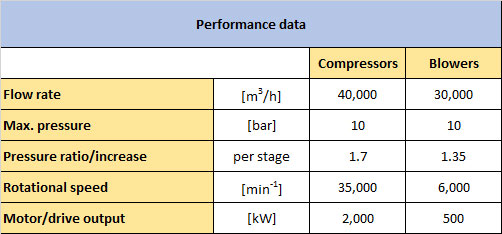
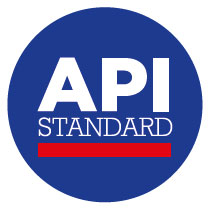